Enhancing Crude Oil Transfers with Fast Loop Automatic Sampling Systems
In the oil and gas industry, an efficient metering system is crucial for crude oil transfers. It not only determines the quantity but also the quality and composition of the oil stream. Utilizing a certified system for both quantity and quality verification when making or verifying a bill of lading is in the best interest of both buyers and sellers. Accurate hydrocarbon accounting helps prevent reputation damage, claims, and unnecessary tax payments. With increasing variations in oil composition and a global shortage, measuring the quality of the stream is essential. No one wants to pay $100 for a barrel of water.
Importance of Accurate Measurement in Hydrocarbon Transport
Pipelines, up to 12 inches in diameter, transport vast amounts of hydrocarbons, representing millions of dollars annually. Accurate watercut measurement is vital. Online devices for watercut determination are commonly used for process monitoring but often lack the precision needed for bill of lading verification. Especially for low watercut streams, achieving accuracy down to a ppm level requires compensating for variables like density, viscosity, salinity, and sulfur content to avoid inaccurate readings. Additionally, there’s no internationally recognized standard for certifying these instruments. For these reasons, automatic sampling systems are used for custody transfer purposes.
Advantages of Automatic Sampling Systems
Accuracy and Performance
Traditional automatic samplers assume a homogenous flow in the pipeline, overlooking variations in droplet size, density, and viscosity. Inline automatic sampling systems with small inlets may miss larger water droplets, making samples unrepresentative. Even small pipelines can have saturation issues, causing water to travel at the bottom and bypass the sampler inlet. An effective solution ensures that the collected sample is representative, regardless of droplet size.
Reliability and Performance
Refineries, storage terminals, and offshore locations aim to reduce operational and maintenance costs. However, low-cost automatic samplers often have high failure rates, leading to high maintenance costs and frequent part replacements. Logistics for repairing samplers can be costly, and custody transfers using unreliable equipment can affect the accuracy of the bill of lading. A reliable, easy-to-use solution with a low failure rate is needed.
KPS Fastloop Sampling Systems
The KPS Fastloop Sampling System, depending on process conditions, may require inline mixing to ensure a homogenous flow. Static mixing devices are commonly used for smaller pipelines, though they can cause pressure drops and reduce throughput. In such cases, the KPS e-Jetmix™ system might be a better option.
The KPS Fastloop Sampling System features an external pump and a specially designed Take-off/Return probe. The fastloop circulates a portion of the main stream using the KPS Take-off/Return probe. In the fastloop, the innovative and sustainable CS-01 cell sampler accurately collects 1cc sample grabs and transfers them to receiver cans. Notably, the system allows for isolating the sampler or online devices for maintenance without shutting down the process.
CFD Modeling for Precision
Dealing with variations in densities, viscosities, and flow rates, KPS utilizes advanced CFD modeling software to verify installation design. This tool accurately predicts pipeline behavior across the operating envelope, ensuring precise results for customers.
Minimize Cross-Contamination
Traditional inline samplers often have significant distances between the sampler and receiver cans, increasing the risk of cross-contamination between batches. The KPS Fastloop Sampling System, or the efficient KPS e-Jetmix™ Sampling System, places the CS-01 cell sampler just above the receiver cans, minimizing contamination and preventing water traps in U-bends.
Sustainable Heavy Duty Sampler
The KPS Fastloop Sampling System is optimized for low maintenance and sustainability. The innovative KPS CS-01 cell sampler boasts a high mean time between failure rate, reducing operational and logistical costs. This heavy-duty automatic sampler handles heavy crude oils with high solid contents and highly viscous crudes, maintaining performance despite process variations.
By integrating these features, the KPS Fastloop Sampling System provides reliable, accurate, and sustainable solutions for crude oil sampling, ensuring quality and efficiency in every transfer.
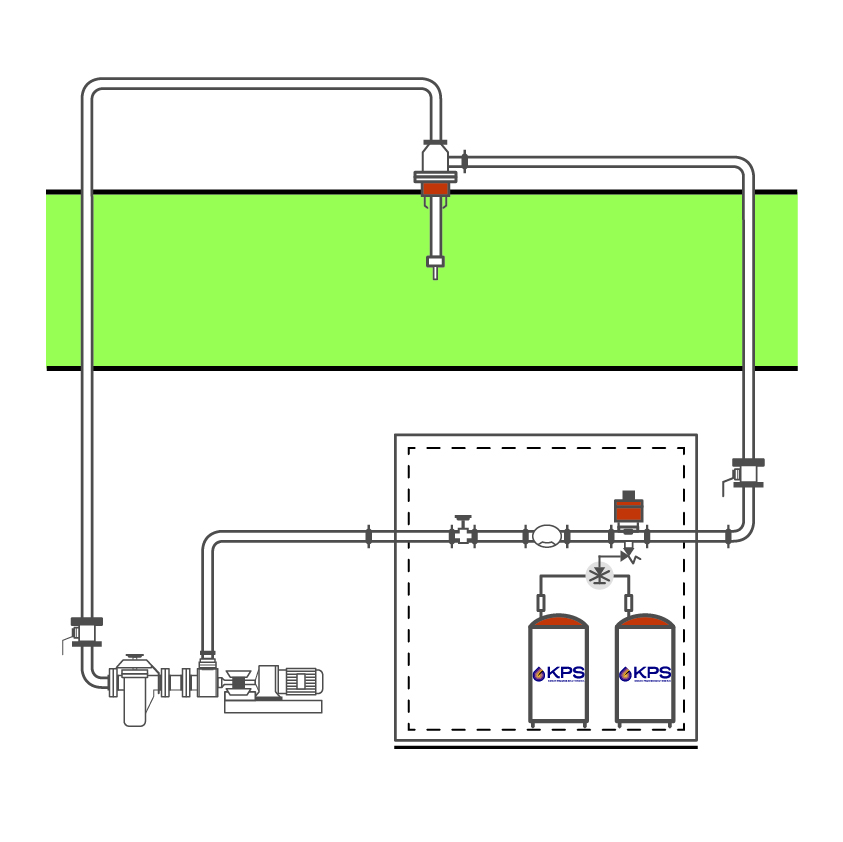
KPS e-Jet-Mix™
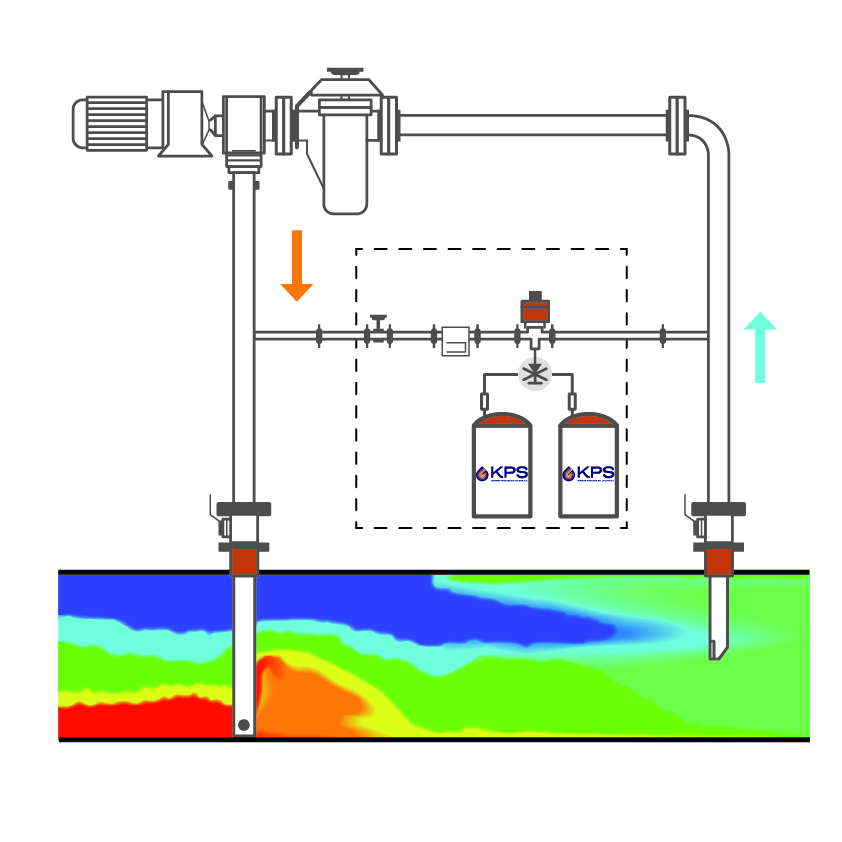
Fast Loop
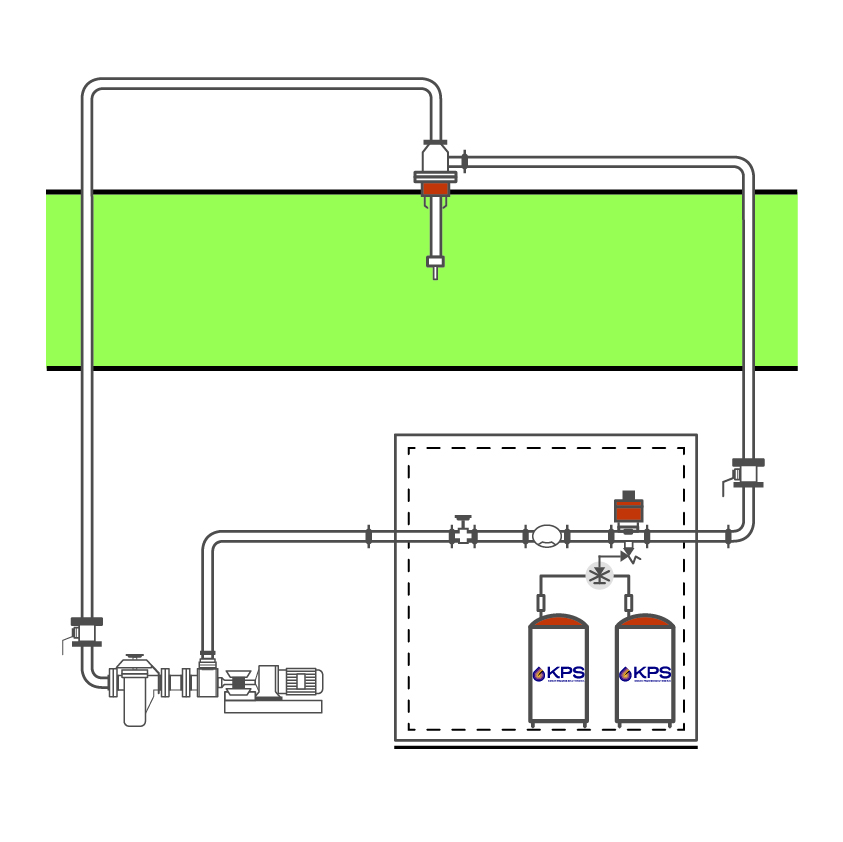
Probe Sampler
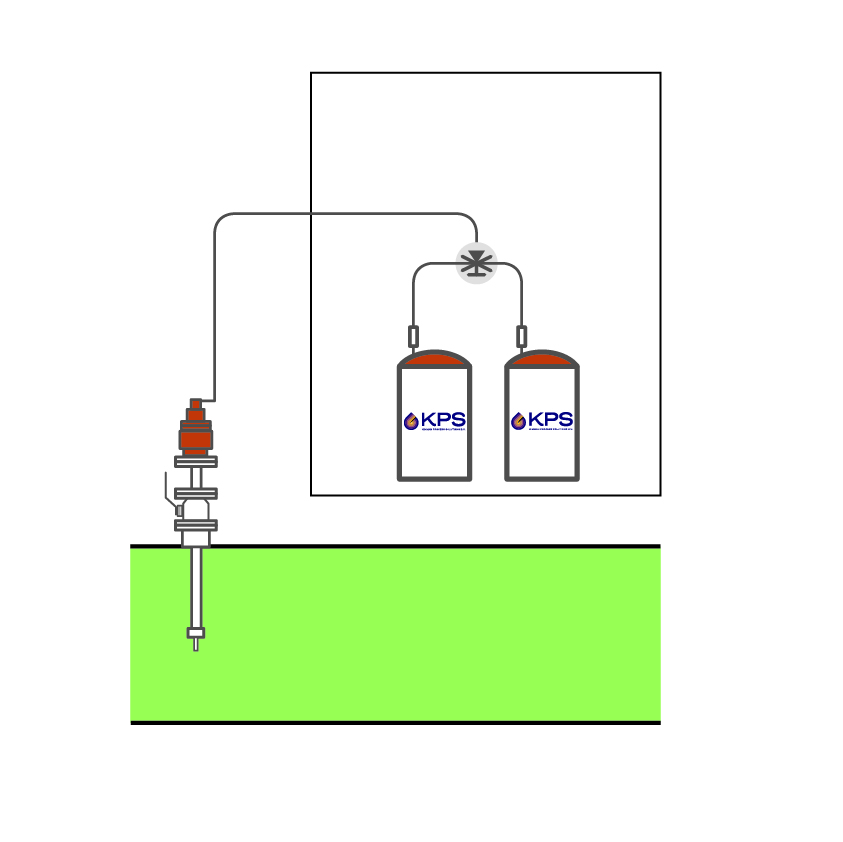
Multiphase Sampler
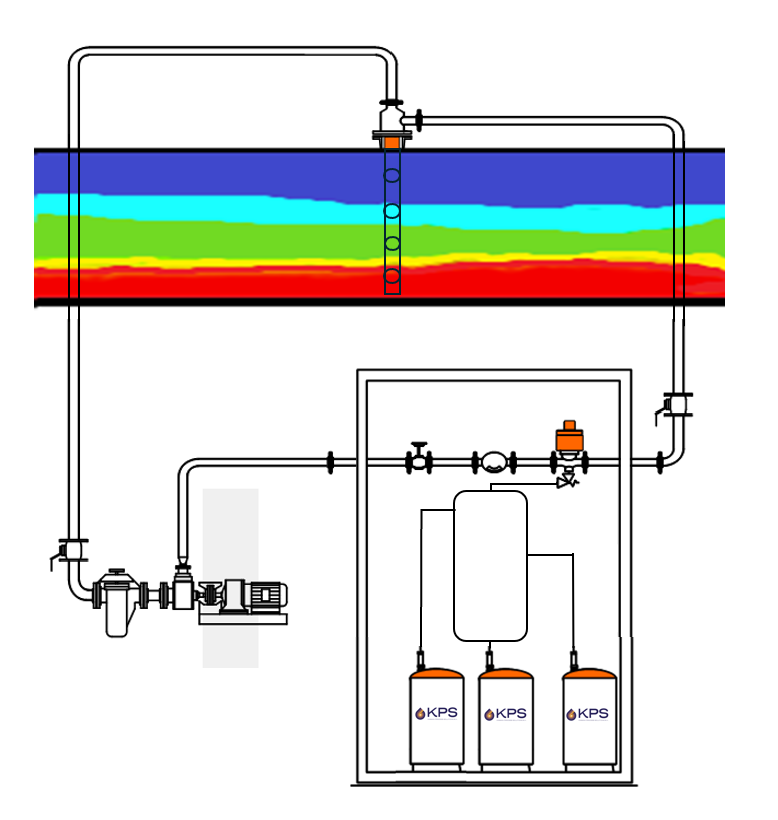
Get in contact with our experts!
Send your e-mail and we’ll get in touch!